How not to make an anvil:
The wrong way to try to make a blacksmiths anvil
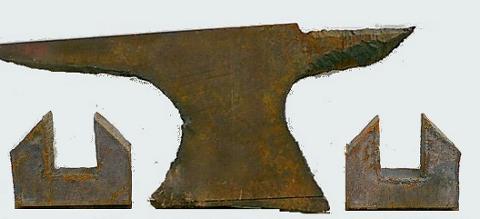
These are parts that were given to a friend to make an anvil from. He went as far as borrowing my heavy angle grinder and looking at this mess. . . then gave them back. It was the right decision.
The problems start with the fact that there was no pattern or lines to cut to. The results are the shape above. You really need to know what an anvil should look like or have some design and drawing skills before you start. If you have to look at the photo above for more than a few seconds to know what is wrong with the shape then you have no business trying to make an anvil.
Then there is the quality of the flame cutting. It is actually worse than it looks in these photos. Flame cutting is an art that takes a lot of practice. If you cannot cut a relatively smooth straight line do not start one of these projects. If you know someone else that is good with a cutting torch, ask them to do the cutting. The best thing to do is make a CAD drawing and have someone with a machine torch do the job. However, you can also do some cutting with a track torch or a Hob-O (circle cutter).
You could spend a week trying to clean this up with a grinder and in the end still have a mess and the awful shape.
Finally, the 2″ plate, while quite heavy is not serious anvil making material for this type design. It could have been put to much better use in other ways such as the top plate and a body under that.
Concrete is not a suitable anvil material. See Anvil Making, Concrete
Making anvils is not for everyone. However, as some of our other articles show a teenager with a good eye, some support from his brothers and some metal working skills can do a wonderful job. Making anvils is metal sculpture on a fairly large and heavy scale. It is an art.
It was welded at 550 amps for deep penetration. The anvil has a ring like the bells of St. Mary’s. It has a nice rebound comparable to an early Mousehole anvil. The anvil weighs 128 lbs. The horn is pinned and has a supporting weld.
The overall length is 24 1/2″, 17 3/4″ long face including tapered horn, 4″ wide face, 4″ x 6 3/4″ conical horn, 8 1/2″ tapered horn that is 1″ wide at the tip, 1″ Hardy Hole & Pritichel Hole, 4 1/4″ high body with 2 5/8″ base, total height 6 7/8″, 7 1/8″ wide x 10 1/4″ long base.
The base also acts as a upsetting block. Instead of a side horn I decided I will make a bridge hardie.